GRZ Technologies builds metal hydride hydrogen storage modules according to a patented design on its own production lines. The design of the DASH storages is highly modular and leads to outstanding technical properties. Combined with highest quality standards, this sets the benchmark in solid-state hydrogen storage.
Inner workings #
The basic component of each storage module is the application-specific and optimized hydrogen carrier
material. The material selection and the quality control of the used materials are the responsibility of
our team of material scientists. GRZ uses specialized measurement devices developed and built in house for the necessary characterization and quality control.
Optimized pressure vessels #
Once we have identified the perfect storage material for a project, we manufacture and insert it into optimized stainless-steel containers (e.g., made of AISI 304L3.1). The smallest unit in the modular design used for this is the cell. The cells have different diameters and lengths, depending on the technical requirements. A number of individual cells builds a register. Registers, in turn, are connected to so-called stacks. Each stack is a certified pressure device and made according to the EU Pressure Equipment Directive 2014/68/EU or another applicable standard. The figure below shows a typical stack (M-series):
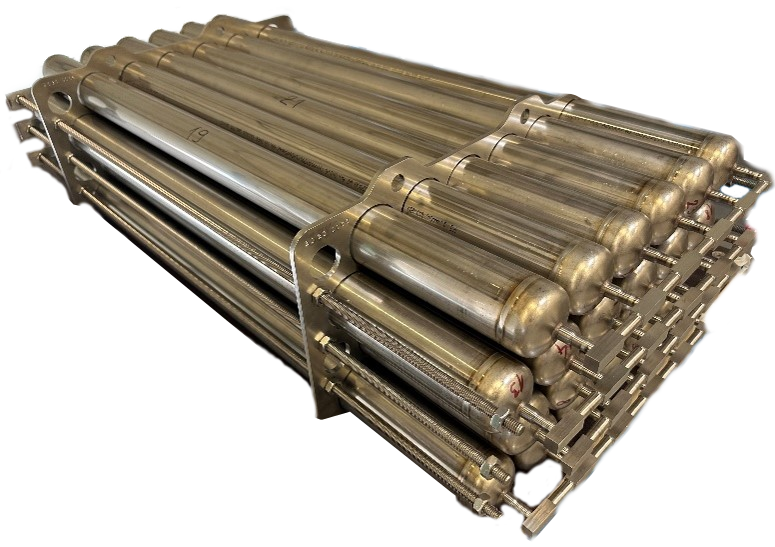
Processes #
GRZ Technologies uses specially optimized welding processes to manufacture the storages. Thereby, we pay particular attention to high quality and repeatability of the process. The objective is to reach a very long service life. For our customers, this means that the storage systems do not limit the lifespan of the projects. It can be operated practically maintenance-free over the entire service life.
Quality control and system design #
After completion, each stack undergoes specifically developed quality control procedures. In particular, we test pressure resistance and tightness quantitatively. Once a stack has passed the strict quality control processes, it is loaded with hydrogen. Finally, we combine stacks into a system with the storage capacity required by the customer. Depending on the requirements, we install auxiliary systems to achieve the desired heat exchange rates.